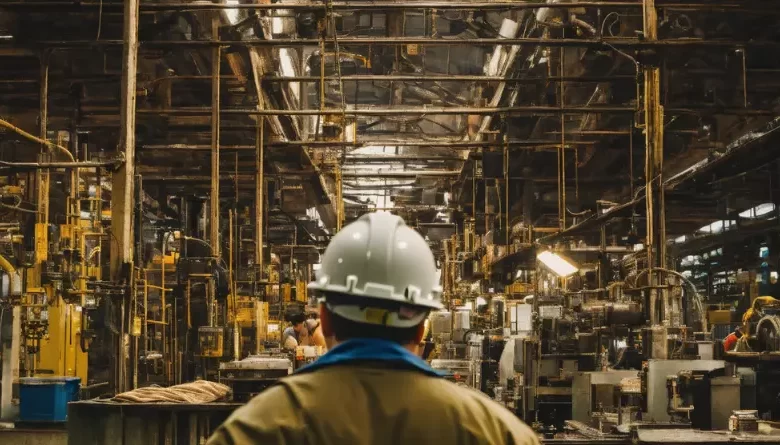
How Can Manufacturers Boost Their Productivity?
Manufacturing companies always strive to find clever ways to work more efficiently, aiming to boost profits and minimize costs. Here are some of the most successful strategies they employ.
Outsourcing:
Outsourcing is a smart strategy that helps companies save both time and money. It enables businesses to stay competitive by letting them concentrate on what they do best instead of spreading themselves too thin.
Manufacturers often choose to outsource various production tasks. For instance, some companies require coil coating for pre-painted metal to prevent corrosion after painting. While this method is the most cost-effective way to pre-paint aluminum and steel substrates, not every manufacturer has the resources, budget, or space to carry out this process. The solution lies in outsourcing to a third party, whether it’s within the country or internationally, depending on the specific parts that need coating.
Another way manufacturers leverage outsourcing is by assembling parts through hired teams, and these pre-assembled parts are then used in the final product manufacturing. If the assembly process can be done economically, shipping the parts back to the manufacturer becomes a viable and cost-effective option.
Predictive Maintenance:
In the world of manufacturing, the smooth functioning of equipment is crucial, and any glitches or breakdowns can seriously harm a business. This can lead to legal issues, increased expenses, damage to reputation, subpar end products, and unhappy customers.
When machines unexpectedly break down, it creates a major disruption in a company’s operations. The unplanned breakdowns often result in costly repairs, forcing companies to halt their activities. If the equipment can be replaced swiftly, downtime can be minimized. However, certain pieces of machinery come with hefty price tags, and companies may not have spare ones readily available.
Every minute, hour, and day that a machine is out of commission translates to lost productivity and profits for the company. A proactive solution to this problem is the implementation of predictive maintenance.
Predictive maintenance is a forward-thinking approach that relies on condition-based monitoring, using sensors and data analytics to detect potential mechanical issues before they escalate. With this system in action, early warning signs of failure are identified, and thanks to machine learning, potential breakdowns can be predicted.
The key advantages of predictive maintenance include increased equipment uptime, lower maintenance costs, improved customer satisfaction, and ultimately, higher profits.
Automation:
Automation is present in almost every industry, but it becomes crucial for maintaining productivity in manufacturing. Robots, for instance, can perform tasks beyond human capabilities, making certain processes safer, especially those that may be too risky for human workers.
By automating essential processes, manufacturers can gain more productive hours, cut down on costs, and enhance overall efficiency and speed. Automation is particularly useful for streamlining repetitive and hazardous tasks and is adaptable to various applications.
In today’s business landscape, many companies follow the Just-In-Time (JIT) principle, eliminating the need for massive stockpiles of parts or inventory. Instead, necessary components and products are produced continuously as required, ensuring a consistent flow of goods while making costs more transparent. Automation plays a vital role in the success of JIT, as the demands are often too high for humans to keep up.
For companies that prefer to handle operations internally, automation is a valuable asset. It reduces lead times associated with outsourcing and increases production output. Unlike humans, robots don’t require breaks, don’t get tired or sick, and can work without constant supervision. With their speed, robots contribute to faster production, allowing companies to recover the costs of implementing automation relatively quickly.
Streamlining Operations:
Boosting operational efficiency involves simplifying operations, cutting out wasted resources, and eliminating unnecessary processes. This involves effective inventory management and optimizing how resources are used.
Many companies find themselves bogged down by inefficient workflows that waste resources. To address this, manufacturing companies often scrutinize workflows, experimenting with changes to identify where the most significant improvements can be made. Training frequently plays a vital role in overcoming this challenge.
The efficiency of workflows often depends on an individual’s training. If employees are not familiar with the correct procedures, they may develop their own methods. Given that employees have a significant impact on a company’s production efficiency and product quality, effective training becomes absolutely essential.
When it comes to procuring raw materials, companies perform best when their needs are predictable, and supplies are readily available. Sometimes, it becomes necessary to switch suppliers or order larger quantities of frequently used items.
Enhancing operational efficiency involves various aspects. While automation, outsourcing, and predictive maintenance are critical elements, the strategies outlined in this article represent just a few of the methods manufacturing companies use to enhance efficiency. While some approaches may overlap, there are also industry-specific strategies.
The manufacturing industry can indeed be profitable if companies maintain efficiency by implementing the right systems and minimizing time and expenses on factors that hinder progress.
Boosting Operational Efficiency Involves Various Aspects
Operational efficiency depends on factors like automation, outsourcing, and predictive maintenance. The strategies discussed in this article are not the only ones manufacturing businesses employ to boost productivity, though. There are industry-specific tactics in addition to the many overlaps.
If a firm maintains efficiency by putting in place the proper processes and spends less time and money on things that slow the company down, manufacturing can be a successful industry.